近年來(lái),三一集團(tuán)緊跟《中國(guó)制造2025》戰(zhàn)略部署,積極推進(jìn)兩化融合體系工作,形成了智能化制造、裝備智能化、智能服務(wù)的完整產(chǎn)業(yè)鏈模式下的集成示范應(yīng)用。集合優(yōu)勢(shì)智力資源,打造智能工廠建設(shè)。
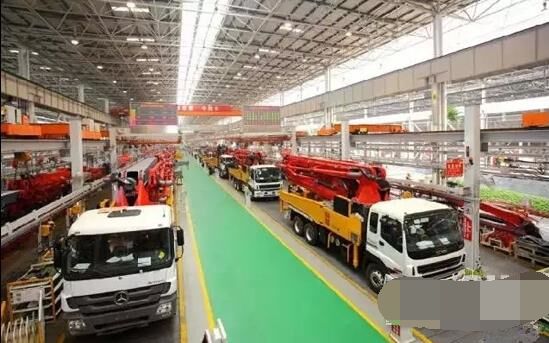
聚集資源 形成全產(chǎn)業(yè)鏈集成示范應(yīng)用
三一集團(tuán)數(shù)字化車間/智能工廠相關(guān)技術(shù)的應(yīng)用示范,一是面向精益制造的數(shù)字化車間。通過(guò)全三維環(huán)境下的數(shù)字化工廠建模和工業(yè)設(shè)計(jì)軟件以及產(chǎn)品全生命周期管理系統(tǒng)應(yīng)用、多車間協(xié)同制造環(huán)境下的SanyMES,實(shí)現(xiàn)計(jì)劃與執(zhí)行一體化、物流配送敏捷化、質(zhì)量管控協(xié)同化。
企業(yè)資源計(jì)劃系統(tǒng)實(shí)現(xiàn)了人、財(cái)、物、信息的集成一體化管理,基于物聯(lián)網(wǎng)技術(shù)的多源異構(gòu)數(shù)據(jù)采集和支持?jǐn)?shù)字化車間全面集成的工業(yè)互聯(lián)網(wǎng)絡(luò),驅(qū)動(dòng)部門業(yè)務(wù)協(xié)同與各應(yīng)用深度集成。
自動(dòng)化立庫(kù)/AGV、自動(dòng)上下料等智能裝備的應(yīng)用,以及設(shè)備的M2M智能化改造,初步實(shí)現(xiàn)了物與物、人與物之間的互聯(lián)互通與信息握手。
二是面向服務(wù)型制造的智能服務(wù)云平臺(tái)。以設(shè)備運(yùn)維過(guò)程數(shù)據(jù)和生產(chǎn)過(guò)程數(shù)據(jù)為基礎(chǔ),形成大數(shù)據(jù)分析與決策平臺(tái),以“互聯(lián)網(wǎng)+”為創(chuàng)新工具,形成了客戶和產(chǎn)品的360度分析,通過(guò)CRM、互聯(lián)網(wǎng)產(chǎn)品、ECC、客戶互動(dòng)中心、大數(shù)據(jù)分析平臺(tái),全面提升客戶洞察、營(yíng)銷互動(dòng)、配件服務(wù)、融資債權(quán)、調(diào)劑租賃等服務(wù)的管理水平。
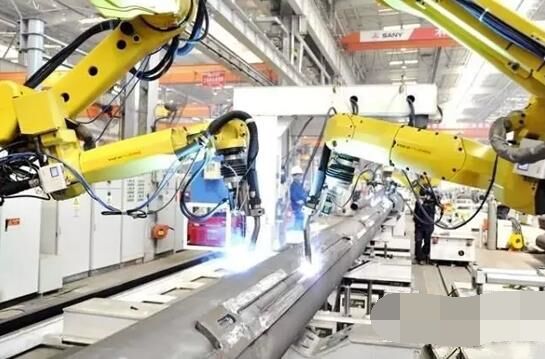
精益管控 大幅度提高自主研發(fā)能力
全產(chǎn)業(yè)鏈?zhǔn)痉稇?yīng)用大幅度提高三一集團(tuán)自主研發(fā)能力,實(shí)現(xiàn)了三一集團(tuán)全球研發(fā)體系的協(xié)同,新研發(fā)產(chǎn)品平均每年增加52件,新增知識(shí)產(chǎn)權(quán)142項(xiàng)/年,研發(fā)周期平均縮短1.5年,研制周期縮短30%。
通過(guò)數(shù)字化車間建設(shè),實(shí)現(xiàn)對(duì)整個(gè)生產(chǎn)過(guò)程的精益管控,大大提高產(chǎn)品制造過(guò)程的質(zhì)量、物流、生產(chǎn)管控程度,企業(yè)生產(chǎn)效率提高24%以上,生產(chǎn)周期縮短28%,減少導(dǎo)致生產(chǎn)的誤操作40%,不良品率下降14%,物流運(yùn)作效率提高18%以上,送貨速度提高12%;節(jié)省人力成本約20%,總體制造運(yùn)營(yíng)成本降低28%,生產(chǎn)節(jié)能7%。
三一集團(tuán)通過(guò)面向服務(wù)型制造的智慧服務(wù)體系建設(shè),可持續(xù)提升在售后服務(wù)環(huán)節(jié)上的高效、貼心的形象。將使得可跟蹤追溯的物料達(dá)到90%以上,異常事件響應(yīng)時(shí)間縮短60%,訂單按時(shí)交付率提高15%,總裝質(zhì)量問(wèn)題可追溯率100%,企業(yè)服務(wù)型收入占比將進(jìn)一步提高至68%,比原來(lái)的提高8~10%。
為保障通訊的安全性與再創(chuàng)新的可持續(xù)性,在三一集團(tuán)面向工程機(jī)械裝備全生命周期的數(shù)字化制造與智能服務(wù)平臺(tái)中,裝備自主與國(guó)產(chǎn)化率超過(guò)72%,產(chǎn)品自主與國(guó)產(chǎn)化率超過(guò)85%,軟件的自主及國(guó)產(chǎn)化率超過(guò)70%。
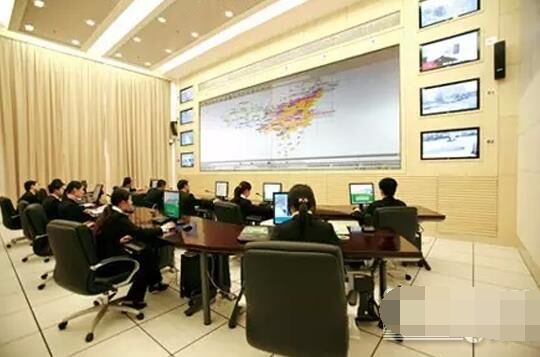
三一集團(tuán)在數(shù)字化車間、智能裝備、智能服務(wù)三個(gè)方面的總體規(guī)劃、技術(shù)架構(gòu)、業(yè)務(wù)模式、集成模型等方面進(jìn)行有益的探索和應(yīng)用示范,為工程機(jī)械行業(yè)開(kāi)展類似應(yīng)用提供了一個(gè)很好的范式,不僅有助于工程機(jī)械行業(yè)通過(guò)信息化的手段和先進(jìn)的物聯(lián)網(wǎng)技術(shù)來(lái)加速產(chǎn)品的升級(jí)迭代,而且促進(jìn)行業(yè)通過(guò)開(kāi)展數(shù)字化車間/智能工廠的應(yīng)用實(shí)踐來(lái)完成企業(yè)創(chuàng)新發(fā)展。
【推薦】
【市場(chǎng)】工程機(jī)械新紀(jì)元:電商之路
【獵奇】夠膽!只穿衣服就敢從幾千米高
【社會(huì)】青島九大教育指標(biāo)列副省級(jí)城市